Control of electrical drives
This research project is not currently active and this page is not regularly updated. It is provided here for archival purposes.
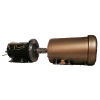
The optimization of the operations of electrical drives is a topic of paramount importance when considering energy efficiency of industrial plants. An electrical drive consists of a converter and a motor: this architecture allows one for variable speed control of these machines. These devices convert the electric energy from the grid into mechanical energy in the load. The goal of the research activity is the minimization of the power losses in the transformation. In particular, we focus on accurate modeling and control based on mathematical optimization to improve the performance of the drive. The activity is in the framework of the Energy SmartOps project.
The operations of electrical machines are responsible for around 45% of the total global electric power consumption. Thus, any improvement of their efficiency can result to be extremely beneficial in terms of power savings and emissions reduction. The goal of the research activity is to develop control techniques for electrical motors, driving loads as compressors or pumps, that minimize power losses. In particular, we focus on accurate modeling of the machine losses and load characteristics to derive optimization based control techniques that improve the performance of the drive.
The work is in the context of the external pageEnergy Smartops Projectcall_made, which is a consortium of academic and industrial partners for energy optimization of industrial plants.
Research
Industrial electrical drives consist of a converter, which takes three-phase voltages from the grid and converts them in desired three-phase voltage shapes, an electrical motor and the load. This allows to operate the machine at variable frequency, which is in general required by the industrial processes.
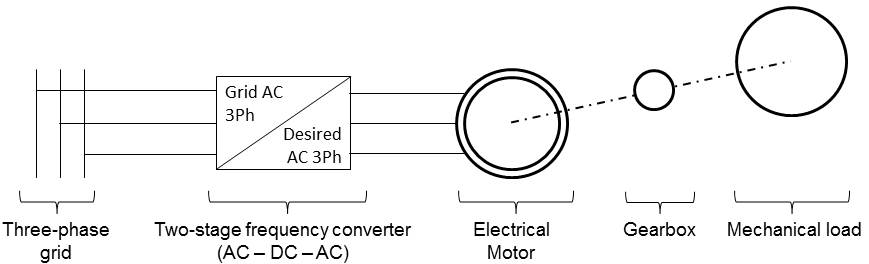
To simplify the analysis of the problem, we initially focus on induction motors, that are the electrical machines with the highest potential for savings. Hence, we assume that the input variable of the system are the motor stator currents, and that we are able to relate them to the opening status of the inverter switches inside the converter, i.e. the real input of the system, through Space Vector Modulation techniques.
The operation of the motor is normally in a region where some non-linearities occur, due to the magnetic effects which constitute the basis of the machine working. Magnetic hysteresis takes place continuously in the ferromagnetic material, causing saturation of the machine at high flux and cyclic energy losses. Hence, a detailed model of these phenomena is needed to control the machine.
Constructors, in general, provide only some empirical and inaccurate data about the machine saturation. Some empirical formulas allow to get an approximation of the energy losses, but they result to be quite inaccurate, since they do not account for the physical phenomena that occur in the motor.
Hence, we propose a systematic procedure to identify the hysteresis in induction motors, which is derived from the physics and consider microscopic ferromagnetic effects. In case of a simple magnetic specimen, indeed, the Jiles-Atherton model lets one find accurately a mathematical relation for hysteresis loop, derived from the physics. We extend that theory to induction motors and introduce an experimental algorithm to determine the hysteresis curve in the machine, which uses only the available voltage and current measurements from the inverter. In this way, we derive an analytic expression for the magnetic saturation and the hysteresis losses.
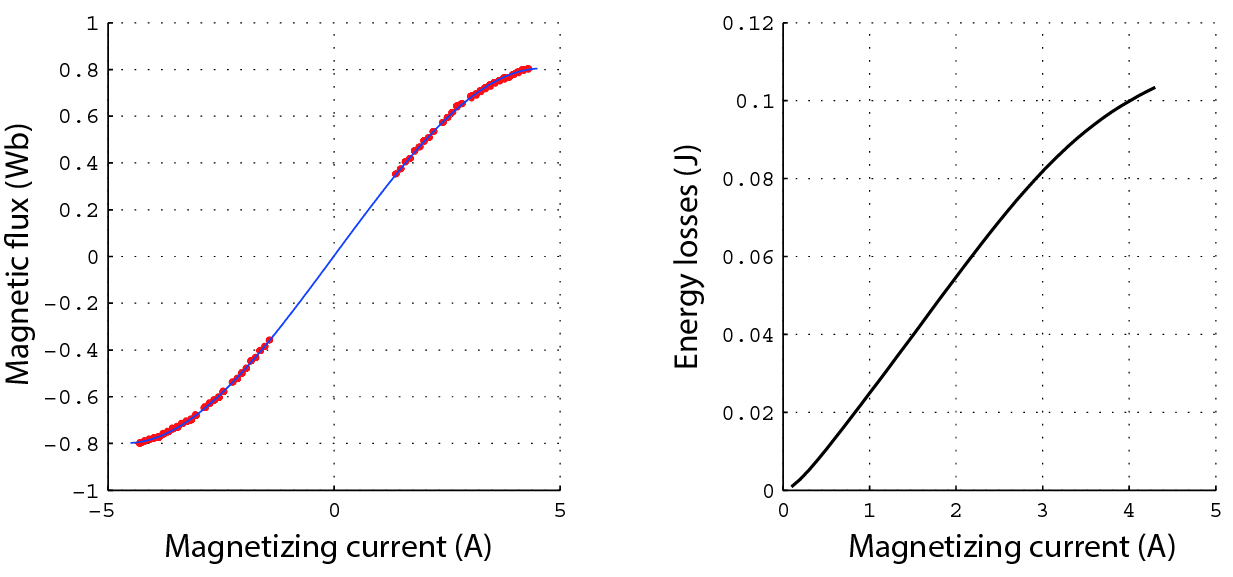
The aforementioned results make the flux and velocity estimator more accurate. Furthermore, they can be adopted in optimization algorithms that find the control law which minimize the power losses to obtain a certain torque. The problem can be proven to be convex in its domain and can be efficiently solved. For the motor under test, the power losses reduce of 27% with respect to the state-of-the-art control, with a corresponding improvement in the efficiency of 3%.
Related publications
- High-Bandwidth Explicit Model Predictive Control of Electrical Drives
- An accurate extended Kalman filter scheme for the reduction of the flux angle tracking error in sensorless induction motor drives
- Application of advanced nonlinear control concepts to induction motor drives
- Optimal control of a high efficiency low distortion 6-level hybrid multilevel motor drive
- Sensorless Explicit Model Predictive Control of Permanent Magnet Synchronous Motors