Chemical processes
This research project is not currently active and this page is not regularly updated. It is provided here for archival purposes.
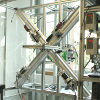
The chemical industry, a pillar of the world economy, has been known to profit from modern control techniques, such as model predictive control, for decades; however, the complex and highly nonlinear nature of certain processes has so far eluded useful quantitative description and hence has been difficult to control. The field of separation processes contains many such problems, and in recent years, the automatic control laboratory has focused its efforts on these types of systems: Apart from several contributions in the field of chromatography, in particular the control of simulated moving bed (SMB) processes, research is mostly connected to the CrystOCAM project.
The CrystOCAM (Crystallization: Optimal Control and Advanced Monitoring) project is a collaboration between the laboratoire automatique at EPF Lausanne and the separation process laboratory at ETH Zurich, that aims at developing a new generation of tools to model, to measure and monitor online, to optimize and control the distribution of sizes and shapes of crystals of a suspension of particles and crystals during the crystallization from solution.
The CrystOCAM project was funded by the external page Swiss National Science Foundation (project number 135218).
Research
Introduction
The importance of crystallization in the pharmaceutical, food and fine chemical industries stems from its ability to yield highly pure solid products. Beside the final chemical purity, however, the solid state form, the size and the shape of the resulting particles are of paramount importance for the product quality, because they determine characteristics such as filterability, tabletability, flowability and even bioavailability. Practitioners in these industries are well aware of the fact that crystals can take on a variety of shapes, even for the same chemical substance. Any form of control over particle size and especially shape should allow for the design of improved processes. Until recently, however, the optimization of crystallization processes in terms of particle morphology has been hindered by a major obstacle: The lack of reliable, fast and quantitative measurement devices, which prohibited the online monitoring and hence modeling and optimization.
The CrystOCAM project aimed to address these limitations by providing setups and analysis protocols that yield reliable, sensitive and accurate data, which can be used, e.g., for optimization and control. To this end, the CrystOCAM project combined the know-how and tools of three groups at ETH Zurich and EPF Lausanne: The Separation Process Laboratory, headed by Prof. Marco Mazzotti (ETH Zurich), the Automatic Control Laboratory group headed by Prof. Colin Jones (EPFL) and IfA, through Prof. Manfred Morari (ETH Zurich).
System Characterization
An important part of the CrystOCAM project is the characterization of systems whose exact behavior has never been accurately and quantitatively monitored before. To this end, new models for the crystallization behavior of complex-shaped particles need to be created and validated against experimental data. Within the scope of this project, a variety of effects has been investigated, ranging from simple, size independent growth mechanisms to studies of growth rate dispersion or agglomeration. Apart from the inherent scientific value of this research, the resulting models can then be used as the basis for reachability analyses, process optimization and control, or simply to provide qualitative lessons regarding the presence and location of (un)desirable process conditions.
Optimization and Control
The interest in the optimization and control of particle shape has seen a dramatic rise in research in recent years. With the advent of new imaging tools and efficient numerical algorithms for the modeling of crystal shape, various authors have conducted studies on how to best drive crystal shape towards a desired direction, ex- or implicitly trying to solve the underlying nonlinear, nonconvex optimization task. However, in addition to a notable absence of experimental validation, only a handful of authors has so-far considered the use of novel yet promising process designs to specifically manipulate shape. Such methods could potentially yield a massive enlargement of the attainable particle shape region.
The researchers at ETH Zurich and EPFL possess the technology, experience and know-how to fill the various gaps currently existing in the optimization and control of crystal shape.