Digital fabrication
Digital fabrication
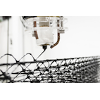
This project investigates the use of robotics in architecture and construction. Our objectives are to design and analyse control systems for cooperative robots engaged in building construction. These robotic systems will allow the construction of architectural designs that are not currently possible due to cost or precision constraints.
Digital fabrication represents a new way of building and is becoming a core discipline in architecture. It is the link between digital design technologies and the real construction process. New architectural designs and structures can thus be realized by using inexpensive precise and resource-efficient on-site robotic construction.
Since 2005, ETH Zurich has taken a pioneering role in the research in digital fabrication. To further intensify investigations in this field, the development of a new external page National Center of Competence in Research (NCCR) "Digital Fabrication" has been funded by the Swiss Federal Department of Economic Affairs, Education and Research (EAER). It represents an ambitious project involving different disciplines as architecture, robotics, systems control engineering, computer-aided design and materials sciences. The interdisciplinary research team is gathered around several professors of ETH Zurich, HSR (Hochschule für Technik Rapperswil), EPF Lausanne, EMPA and Bern University of Applied Sciences.
The Automatic Control Laboratory of ETH Zürich (IFA) is developing new solutions for control systems in cooperative robotics within the project of Digital Fabrication.
Research in Digital fabrication at IfA
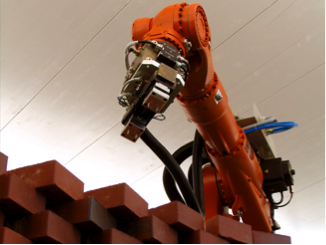
Most of the tasks during the construction process are of collaborative nature, as for example the manipulation of heavy or large objects. Therefore, it is necessary to design multi-agent robotic systems.
Cooperative manipulation
Within a multi-agent robotic system, each robot has a certain degree of information about its own and the cooperating robots' states and acts in order to achieve a common goal. Tasks of the involved autonomous robots may include sensing the environment, planning motion trajectories and ensuring safety of humans on the construction site. The control goal for the robotic system is to achieve good performance in cooperatively accomplishing the assigned task. Hereby, constraints due to hardware restrictions, environment and task accomplishment, as for example limits on interaction forces, have to be satisfied. Different group architectures for cooperative robots are possible:
Centralized control
The control inputs for each robot is computed in a central unit. An important drawback of this architecture is that the system is vulnerable to a single point of failure. Moreover, real-time control requires communication of each robot's system states to the central unit at a suitable frequency, as well as adequate computational power and memory capacity.
Decentralized control
The individual control laws are only based on information about each individual robot's states. Coupling interaction is taken into account as disturbance. This approach is rather conservative and task performance of the overall system is limited.
Distributed control
To overcome the drawbacks of the afore mentioned architectures, the following approach is possible: each robot has information about its own local states and communicates with its neighbors. Neighboring robots are defined by coupling states or coupling constraints between them. The individual local control laws are based on local (distributed) optimization, taking into account local information as well as coupling interactions to neighbors. This approach is most promising in terms of task performance, modularity of the system as well as robustness to failure. More information on cooperative control can be found here.
Uncertainties
Due to imprecise measuring and modeling, the robot's local information, as for example its kinematic parameters, configuration and dynamics are subject to uncertainties. Moreover, loads and contact forces due to interaction, as well as the positions of obstacles and of the collaborating robots are not precisely known. To face these uncertainties, different control strategies are possible:
Robust control
Robust control strategies are designed to avoid failure in the presence of measurement imprecisions or material tolerances.
Adaptive control
Adaptive control strategies can be used. They are designed to dynamically correct the mathematical model, which does not exactly fit the real system due to inexact parameters or unmodeled dynamics.