Industry 4.0
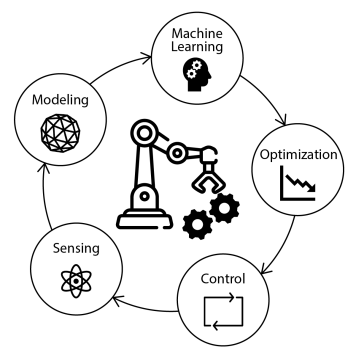
The availability and ease of integration of sensors opens the possibility of utilizing additional data to monitor and control industrial processes for the optimization of processing time and quality. Our group’s research focuses on the integration of advanced control methods in combination with statistical and machine learning insights in industrial equipment. Systems of increased complexity can be controlled using data-driven methods to model their processes without full knowledge of their mathematical representation. Models can be updated with data-based algorithms for learning unmodelled effects during operation. Such methods have been demonstrated in the field of robotics, but have not been widely applied and adapted for implementation in manufacturing. We are currently working on several projects on the intersection between simulation, machine-learning algorithms, model predictive control and statistical methods: plasma spraying optimization, productivity maximization for machine tools and advanced control for precision machining and additive manufacturing. Our approaches are interesting both from a practical point of view – providing enhanced performance of the machines – and from the research point of view: the general questions posed by our applications allow us to explore and design new methods of data-based control. This line of research is part of a long-standing collaboration between inspire AG and the Automatic Control Laboratory.
Research
Plasma spraying optimization
(Xavier Guidetti, Alisa Rupenyan, John Lygeros)
Direct current plasma spraying is a manufacturing method used to deposit coatings on materials to protect them against multiple degradation mechanisms. Currently, the reproducibility of the process remains quite low, as the wear state of the gun and numerous unmodelled factors influence the results. Given the critical applications where plasma sprayed components are used the plasma gun settings are very conservative. This often reduces the economical efficiency of the process and leaves space for optimization.
Our research currently focuses on the application of Bayesian optimization to the plasma gun parameters selection. The coating process is modelled using a Gaussian process model. Based on this, our algorithm suggests the settings for the next batch of experiments to run in order to produce the desired coating. While the state-of-the-art technique requires approximately one hundred experiments to find the desired specifications, our automatic approach is one order of magnitude faster.
The set-up process – in plasma spraying as well as in multiple other industrial processes – is carried on in batches of experiments. In a context where we often face a limited budget of batches and experiments, our research focuses on the dynamical selection of the batches size to optimize the set-up procedure. Our goal is to design an algorithm that is aware of the available evaluations budget and maximizes the amount of collected information with a lookahead approach.
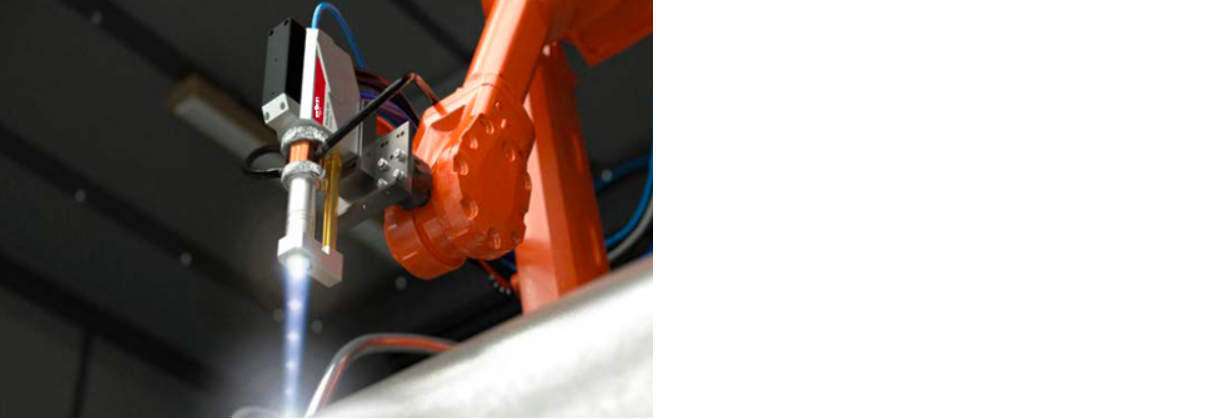
Productivity maximisation of machine tools
(Samuel Balula, Alisa Rupenyan, John Lygeros)
Many manufacturing processes rely on the movement in space of an active tool which is mounted on a high precision, high performance positioning system. A fast, and usually simple, control loop tracks a previously defined reference as accurately as possible. To maximize productivity, it is possible to design carefully the reference provided to the existing control system, given the shape of the trajectory that is desired, the knowledge of the machine operational limits, and a precise model for the system.
Our work focuses on the design of general methods for maximising productivity, with models identified from experimental data, and relying on optimisation techniques to design optimal reference trajectories.
As an example, a laser metal cutter machine, uses a laser beam to cut through a metal sheet. The head focusing the laser is mounted on top of a 2D gantry system. Our algorithms design reference paths that take into account the expected behaviour of the machine, the specified tolerances of the part to be produced, operational limits, such as the limits in acceleration and velocity, and, if they exist, process constraints.
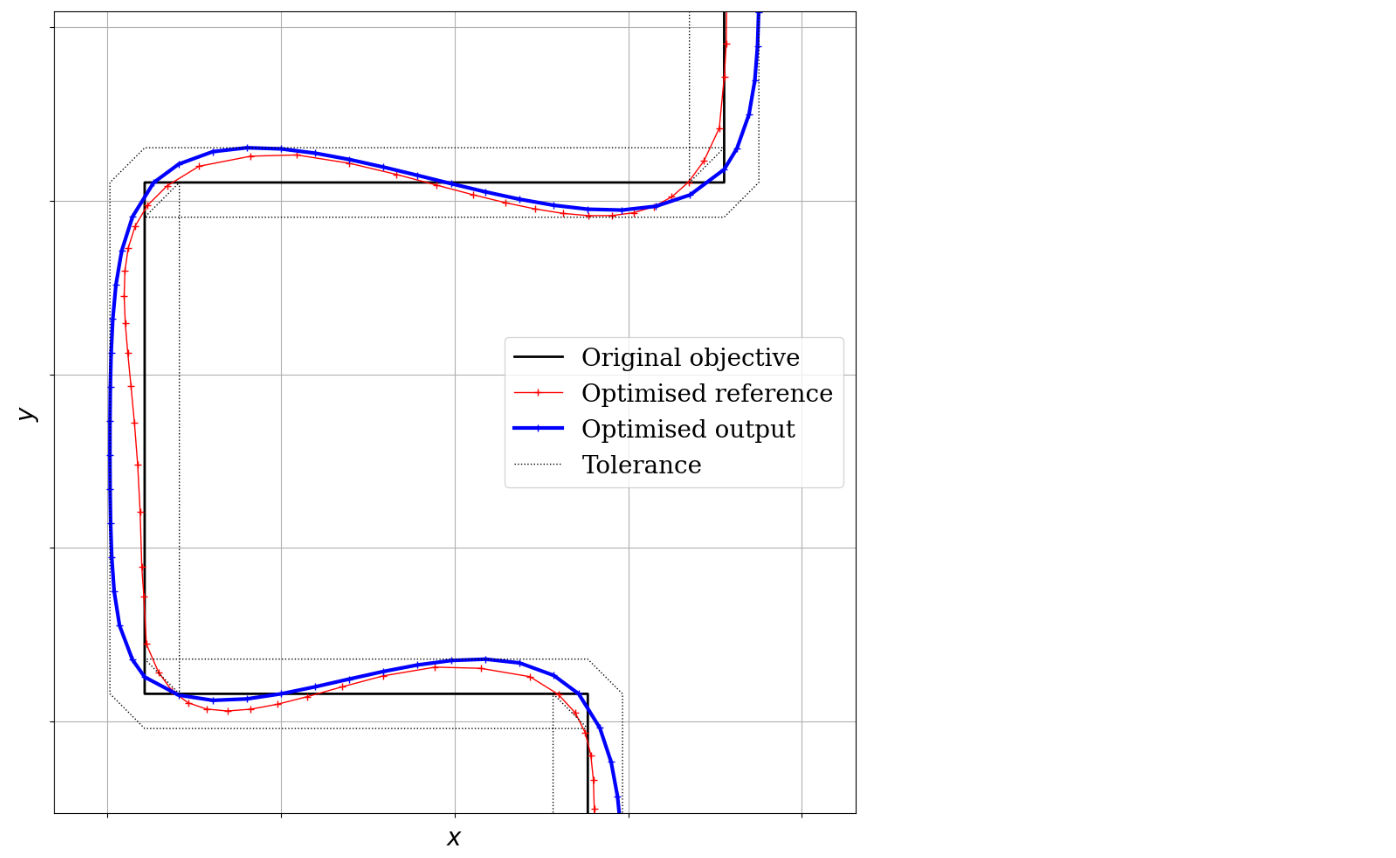
Advanced Control for Additive Manufacturing
(Dominic Liao McPherson, Alisa Rupenyan, John Lygeros)
Manufacturing tasks are often repetitive, involving the same processing steps being repeated over and over to produce many identical parts. This makes them well suited for data-driven methods that exploit repetition, similar to those developed for autonomous racing. In additive manufacturing (AM) technology a laser is used to melt powdered plastic material into a solid structure based on a sliced 3D CAD model. Controlling the laser power and other process parameters between the deposition of different layers in closed loop ensures that the quality of the produced part will achieve a significantly reduced variation, while productivity is maximized.
We aim to optimize laser power and scanning speed with a predictive control approach such as model-based predictive control (MPC), considering the layer-to-layer dynamics, in combination with iterative learning control techniques. Furthermore, since the process is complex to model based on first principles, it will be learned from real-time process data, in combination with FEM-based simulation of the process. New theoretical methods will be developed to address control on various spatial and temporal scales, including layer-to-layer feedback.
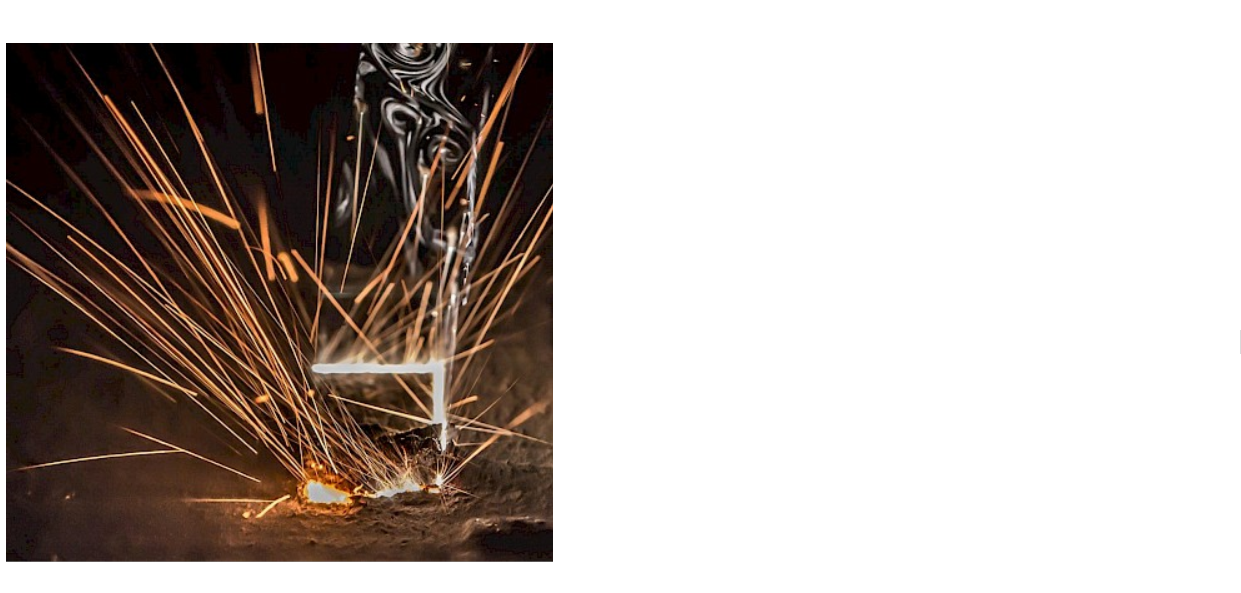
Publications
M. Khosravi, V. Behrunani, P. Myszkorowski, R. S. Smith, A. Rupenyan, J. Lygeros. external page Performance-driven cascade controller tuning with Bayesian optimization. Under review.
S. Balula, A. Liniger, A. Rupenyan and J. Lygeros. external page Reference design for closed loop system optimization. European Control Conference (ECC), pp. 650-655, 2020.
A. Liniger, L. Varano, A. Rupenyan and J. Lygeros. external page Real-Time Predictive Control for Precision Machining. IEEE Conference on Decision and Control (CDC), pp. 7746-7751, 2019.
People
Professor, Head of Automatic Control Laboratory
-John Lygeros
Senior Scientist
-Alisa Rupenyan
Postdoc
-Dominic Liao McPherson
PhD-candidates
-Samuel Balula
-Xavier Guidetti
Presentations
• Alisa Rupenyan, “Real time predictive control for precision machining”, presentation at the IEEE Conference on Decision and Control, Nice, France, December 2019. Joint work with Alex Liniger, Luca Varano, and John Lygeros.
• Samuel Balula, Reference design for closed loop system optimization. Presentation at the European Control Conference, Saint Petersburg, Russia, 2020. Joint work with Alex Liniger, Alisa Rupenyan and John Lygeros.
Research supported by
